
靴下をつくる
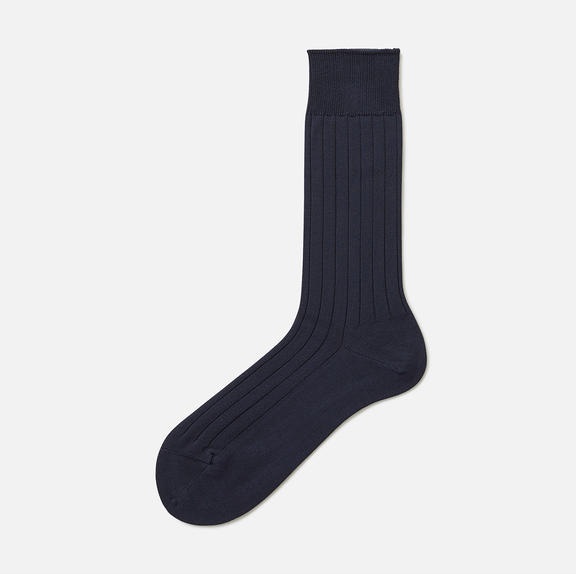
はじめに
タビオの靴下づくりの基本は、柄が入っていない無地の靴下に凝縮されています。
無地の靴下はカラフルな色彩や、華やかな柄物に比べると見せ場が限られています。
しかしその分、靴下を編む職人さんやつくり手、企業の感性や真価が問われ、何よりその姿勢がストレートに商品に現れるのが無地の靴下です。
言わば、
お化粧なしのスッピン勝負。
だからこそ、より細かいところにまで神経を使う気配りが必要なのです。
そして、
上質な素材、注意深く編まれた生地、作り手の気持ちや繊細な心配りから生まれる品格、見た目の美しさ、細部にわたるこだわり––それこそが、タビオの靴下の伝統なのです。
今回はタビオが無地の靴下を作り上げていく過程を、実際にロングセラーとして販売されている商品の完成までを振り返るかたちで紹介していきます。
例として取り上げるのは、メンズ靴下の「メンズ9×2リブビジネスソックス」です。(以下当社品番であり、社内で愛称にもなっている6500と表記)
○ステップ0−狙い
長らくレディース専科としてやってきたタビオが、創業者・越智直正の長年の夢でもあったタビオのこれからを担うことになる「メンズ」市場に進出するのに際し、中心商品として開発に取り組んだのが「6500」でした。
ただ実際に、1つの商品を1から創り上げていくとなると、私たちタビオの社員といえどもなかなか完成図までを見通せないのが現実です。だからまずは、その道の第1人者の元へ相談に行きます。
私たちが訪ねるのはタビオの創業者であり、タビオの物作りの伝統を確立してきた越智直正会長です。(以下、会長)
タビオの靴下づくりは、ここから始まります。
○ステップ1−概略の決定
従来ビジネスソックスといえば薄手のハイゲージ品が中心でした。しかしカジュアルソックスを履き慣れた若いビジネスマンに、こうした薄手の従来品は不評でした。そこでこれに変わるものとして、少し肉厚なミドルゲージの靴下の開発を考えることにしました。
そのために選ばれた工場が西野さん、編み機には針数176本のリブ編機を使うことにしました。
○ステップ2−素材選び
次に素材選びです。
光沢があり、品のある靴下にするため、糸には高級綿のシルケット加工糸を選びました。
原料となる綿の種類については色々な候補の中から、最高級のエジプト綿と、高級アメリカ綿のスーピマ綿という2種類に絞って考えることにしました。
○ステップ3−素材の最終チェック
素材を最終チェックするため、一度会長と相談します。
私たちがこの段階で会長にお見せするのは、まだカカトやつま先部分を編んでいない、また、まだフィット感を出すための伸縮糸を編み込んでいない、素のままの筒編み状態の生地です。
この筒編み状態で、この素材の持っている特性を下記の視点からチェックします。
・面(ツラ)は綺麗か
・ムラはないか
・肌触りはよいか
・編み目は綺麗か
・編み立て性はよいか
・靴下としてのイメージが湧いてくるか
これらをチェックし、素材を最終決定します。「6500」の場合には、上質な光沢やしなやかさを持つシルケット加工をしたスーピマ綿の細番手の糸を採用することにしました。
なお、リブ目(編み地で出す生地の凹凸)は今回の選定編み機の針数と、選んだスーピマシルケット糸の特徴が一番だしやすいものを考えた結果、「9×2」のリブに決定しました。
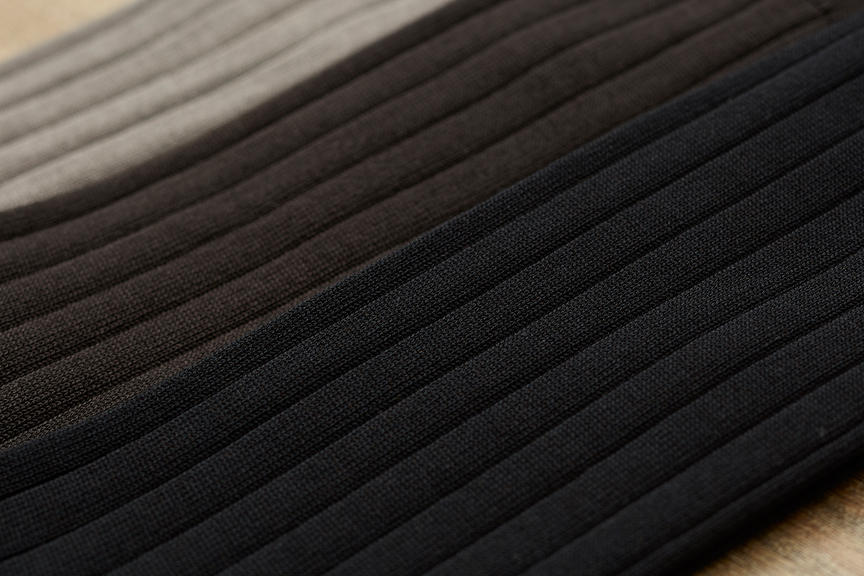
○ステップ4−裏糸の決定
次は裏糸です。
靴下は生地の主となる原料の表糸と、フィット感を出すための伸縮性を出す裏糸を同時に編むことで形成されます。
「タビオの履き心地は、裏糸で決まる。徹底的に研究しろ。なければ開発しろ!」
タビオ商品の品質表示を1度確かめてみてください。ほとんどの商品にポリウレタンという素材が含まれています。非常に伸縮性のある糸で、靴下の裏糸に使われています。
そして、タビオの履き心地を実現するために大きなウェイトを占めているのが、この裏糸の具合なのです。だからこそタビオは、徹底的に裏糸にこだわります。
「6500」の裏糸も、何種類かのものを試し編みした結果、今のものに決まりました。
同時につま先部分の先縫いは機械縫製の「ロッソ」ではなく、足先にやさしく品のある、手作業で1足ずつ行うリンキング仕様に決定しました。
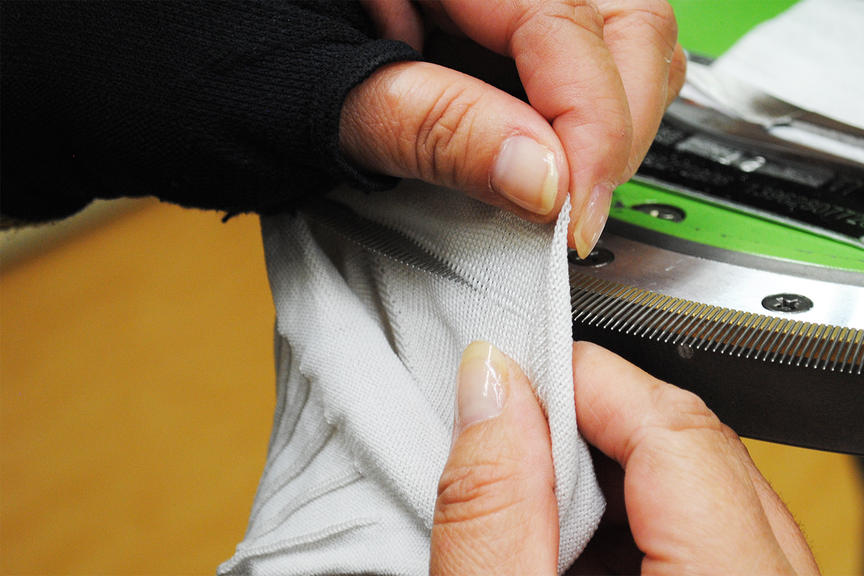
ー手作業で編み目をひとつずつ縫い合わせていくハンドリンキング
○ステップ5−靴下化
以上の段階を経て、いよいよ靴下にしていきます。
タビオの伝統に基づき、改めて
・編み目はきれいに整っているか
・リブはきれいに立っているか
・つま先、カカトのゴアラインのコース数はしっかり入っているか
・総丈は、ゴム丈は、横幅は、ゴム幅はどうか
・全体像に品格はあるか
・裏糸、ゴム糸のカラーはあっているか
・すべての部分の横伸びはどうか
・肝心の履き心地はどうか
以上のチェックが終われば、いよいよ三度、会長の元へ!
○ステップ6―最終チェック
会長による最終チェックを受けます。
越智会長は毎日会社に出社されていますが、商品を見てもらう会長チェックはニッターと商品担当者が夕方出向き、会長宅で受けるというしきたりがあります。
普段から社内を周り一人ひとり話しかけるくらいフランクな越智会長ですが、靴下を目の前にしたこの時ばかりは、流石に緊張感が漂います。
ところでこのチェックを受ける際には、会長の言葉に関する「暗黙の了解」があります。
「これでホンマにええんか」「気になるところがあったらやり直してこい」
こう言われた時は、会長が気に入らなかった時です。この時は、自分たちでどこが悪いのか考えて再チャレンジです。
逆に、
「ちょっと履いてもええか」
そう言われた時、担当者は心の中で「ヤッター!」と叫びます。思わず笑みがこぼれる瞬間でもあります。というのも、ほぼ出来ている場合、少しだけ気になるところがある時に、会長は最終確認のため靴下に足を通すのですが、その際に口にするのがこの言葉なのです。
「まあ、これでええやろ」「ええもん、出来たな」
と言われたら合格。
「何かチョット気になるな」
と言われたら、再度修正し、最終調整をして再び会長宅を訪れます。
合格すれば、いよいよ正式サンプルづくりに入ります。
○ステップ7−品質検査
最後に待ち構えているのが、靴下の品質検査です。
お客様に快適で安全な靴下を提供するために、タビオでは実際に店頭出荷するまでに様々な検査をします。
まずは自分自身で履きます。そして改めて、
・履き心地はどうか
何度も履いて、
・耐久性はどうか
・洗濯するとどうなるか
を自分自身でチェックします。
意外と大切なのは、触っていないサンプルを1日ほど机の上でほったらかしにしておくことです。これで店頭で時間が経った時に、型崩れしないかが判ります。
次に、タビオ奈良にある研究開発事業部で様々な検査・検品を行います。
・堅牢度試験
・湿摩擦試験
・摩耗試験
・摩擦試験
・ピリング試験
・つけ置き試験
・着用試験
・洗濯試験
・各部分の引っ張り試験
・ゴム糸の細部に渡るまで、使用する素材の色の相性はあっているか
などなど、タビオの規格通りの靴下に仕上がっているかどうかをチェックします。
そして合格した靴下だけが、「6500」という商品として認められます。
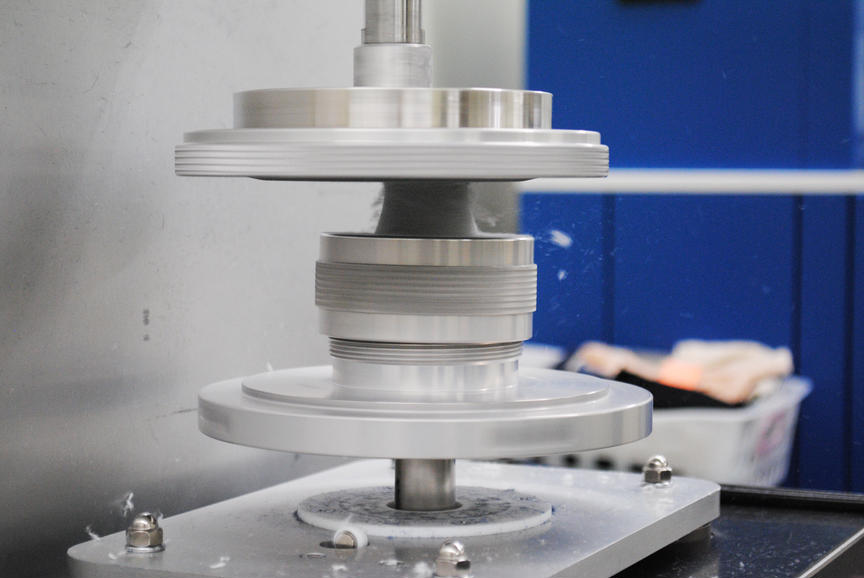
ー生地の耐久性を調べる摩耗検査
さいごに
タビオの伝統に基づいて生まれた靴下は、長い時間をかけた研究と、厳しい検査、そして多くの人たちの手と手間をかけて皆様の元に届きます。
タビオの無地商品は早くても半年、長ければ数年がかりで素材から開発することも少なくありません。
細部までこだわり抜いた靴下たちをお気に召していただけると、これ以上の喜びはありません。